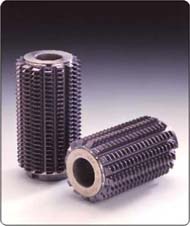
Dual Cut Hob
- Both dry hobbing, which solve environmental problem and conventional wet hobbing are available.
For Dry and Wet Hobbing
- In dry hobbing, cutting speed can be changed faster than that in conventional wet cutting, and tool life is longer as well.
Long Tool Life in Wet Hobbing
- Even if wet hobbing, higher cutting speed and longer tool life are achieved.
Excellent Material
Excellent material for hob having Wear Resistance and Chipping Resistance | ||||||
|
||||||
Optimum Coating in Dry Cutting Optimum Hob Design in Dry Cutting |
Typical structure of chip by wet cutting
Typical structure of chip by dry hobbing
SEM image of adhesive metal on cutting face by dry hobbing
Heat Transmittal and Diffusion
TiCN Coating | ![]() |
TiAlN Coating | ![]() |
Comparison between dry and conventional
HSS Hob | Carbide Hob | ||
Coolant | Non water soluble oil | Dry | Dry |
Speed | 80 – 120 | 120 – 160 | 300 – 350 |
Efficiency | 1 | 1.5 | 3 |
Tool Life | 1 | (2 – 5) | (4 – 10) |
Cost | 1 | (1.5 – 2) | (3 – 4) |
Accuracy | ![]() |
![]() |
![]() |
Reliability | ![]() |
![]() |
![]() |
Workability | ![]() |
![]() |
![]() |
Workshop environment | ![]() |
![]() |
![]() |
![]() ![]() ![]() ![]() ![]() |
Recommended cutting conditions
Summary of dry hobbing
Comparison of wear between Wet and Dry hobbing
m2.5 , PA16°, NT46, no coating on cutting face | |||||||
![]() |
|
Example | Sample 1 | Sample 2 | Sample 3 | |
Work Dimension | Module Pressure Angle No.of Teeth Helix Angle Material |
2.45 17.5 41 25 LH SCr420H |
1.56 14.5 73 30 LH SCM415 |
2.6 20 67 32.5 LH SCr420H |
Cutting Condition | Cutting Method Speed (m/min) Feed (mm/rev) |
Climb Hobbing 105 2.0 |
Climb Hobbing 120 2.3 |
Climb Hobbing 115 2.5 |
Hob Dimension | Outside Dia. No.of Threads No.of Gashes Coating on cutting face |
75 3 12 NON |
75 4 14 NON |
100 5 16 NON |
Comparison of Performance |
Crater Wear (mm)
|
![]() |
![]() |
![]() |
Cost reduction in production ! Dry hobbing is now by newly developed HSS material and coating film ! |
Excellent performance in Dry Cutting comparing to other brand
|
![]() |
Tool life in Dry Cutting is longer than that in Wet Cutting.
|
![]() |
Dry cutting by Dual Cut Hob
![]() dualcuthob.ram (620KB) |
|
||||||||||||||||||||||||