
A unique maker with expertise in both machine tools and cutting tools, to help you respond to demand for more diverse and sophisticated machining, we have developed various technologies and know-how.
Providing overall support for reliable machining that ensures consistent quality, we have proposed processes that meet your needs for MQL and hard finishing and have developed machine tools that embody high speed, high performance, and flexibility.

High-Speed Table-up System for Finishing/Broaching of Extremely Hard Materials
- High-precision Finish Broaching of Materials with High Hardness Level
- Highly Efficient Broaching
- Excellent Workability
- Energy & Space Saving
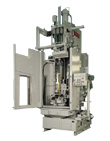
Workpiece transfer type internal processing machines
- The nation’s first and epoch-making workpiece transfer type
- Space saving
Easy installation for space saving by rational layout - Lower working position results in better maintenance and operation.

Workpiece transfer mechanical type internal processing machine
- A power-saving, High-efficiency, High-precision mechanical system
- Compact and space-saving because of pit-free workpiece transfer system and hydraulics are not used
- Realized FMS by ATC and automated setting of cutting conditions

Low-floor type small size general purpose machine
- Internal broaching machine of simple construction and space saving
- High productivity from keyway to spline cutting
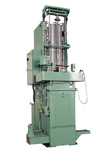
General purpose compatible with heavy cutting machine
- For mass production with multistation available
- High rigidity to withstand severe cutting
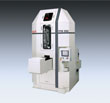
Environment Friendly, Semi-Dry Roll Forming
- Power consumption is reduced by electric power drive and semi-dry rolling.
- High precision roll forming through NC synchronization.
- Change-out procedure is simple.

Environment friendly for energy saving
- Motor drive (elimination of hydraulic system) reduced consumption energy
- Correspond to semi-dry roll forming which requires no coolant
Stable machining accuracy
Compact and space saving
Easy setup change
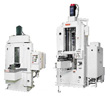
- Most suitable and stabilized rolling conditions to greatly improve machining accuracy
- Compact, energy saving, and low noise NC machines
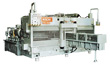
- Cutting accuracy is stabilized even with high load rolling
- Horizontal, rigid machine for high efficiency

Machining System for High Precision Surface Finishing of Crankshaft Bearings
- Space saving
- Energy saving
- Improved maintainability
- Improved Productivity
- Flexibility
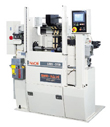
- Roundness is improved by solid back-up stone
- Size control by in-process and post process gauging system
(Option) - Combination of different grit film generates high grade bearing surface
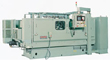
- Roundness is improved by solid back-up stone
- Size control by in-process and post process gauging system
- Combination of different grit film generates high grade bearing surface

- General purpose machine for crank shaft and cam shaft
- Mass production machine configurable in one, two or three stations